Insert Molding
Insert injection molding is the process of forming a plastic part around a different type of material. This is typically done with simple metal objects like a nut or threaded rod. However, insert injection molding can be used to place ceramic parts, other plastic parts, motors, threaded bushings, batteries, or warning labels into the injection-molded part.
The process starts by placing the insert into the mold. Injection molds used in the insert molding process are machined to easily receive and hold the insert. After the insert has been placed, the mold is closed, and the molding process can begin. The mold is filled with molten plastic the same as the regular injection molding process.
What are the Benefits of Insert Molding?
Metal Insert Molding
Are There Special Considerations for Insert Molding?
Support
Can the part design support the insert? The part must have enough material around to insert to hold it securely in place. Thin walls around the insert may result in the insert breaking away from the rest of the part during production, testing or use.
Temperature
Will the insert withstand the temperature of the injection molding process? Temperature must be taken into account when using plastic inserts. The injection molding process uses high temperatures and pressure to produce plastic parts. Be sure that any insert can safely be exposed to the temperature required to melt the plastic injection material. Inserts not rated for high temperature may deform or melt entirely during the injection molding process. It is a good idea to use plastic inserts that have a higher melting point than that of the injected material.
Pressure
Will the insert withstand the pressure of the injection molding process? The amount of pressure generated during the plastic injection molding process is fairly high. Any inserts must be sturdy enough to withstand this pressure without cracking or deforming. The combination of high temperature and pressure can be detrimental to some inserts and should be taken into consideration before the insert injection process begins.
Insert Molding Applications
There are many applications to insert molding. Such applications include:
- Auto industry components
- Industrial equipment components
- Medical devices
- Couplings
- Threaded fasteners
- Electrical parts
Insert Molding Services
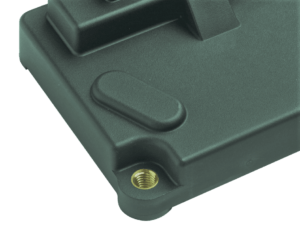